La prevención y gestión de fugas en intercambiadores de calor es crucial para mantener la eficiencia y la operatividad en las plantas industriales.
En este artículo, exploraremos las causas principales de fugas en intercambiadores de calor tubulares y de placas, como el golpe de ariete, y cómo estas pueden ser prevenidas. Analizaremos cómo el diseño de cada tipo de intercambiador afecta la detección y reparación de fugas, y presentaremos estrategias de mantenimiento y operación adecuadas para minimizar estos problemas.
Causas y prevención de fugas en intercambiadores de calor tubulares frente a los de placas
Golpe de ariete: El principal problema de fugas
El golpe de ariete es la causa principal de fugas en intercambiadores de calor tubulares como en los de placas. Este fenómeno ocurre cuando hay un cambio brusco de presión en el sistema, lo que provoca un impacto que puede dañar los equipos. En ambos tipos de intercambiadores, el golpe de ariete puede causar contaminación cruzada, donde el fluido de mayor presión se mezcla con el de menor presión.
Por ejemplo, en el calentamiento de jarabe de azúcar, si la presión del vapor es mayor que la del agua, el vapor se infiltrará en el agua, y viceversa. Esta contaminación es problemática porque afecta la pureza y la eficiencia del proceso.
Fugas en Intercambiadores de casco y tubo
En los intercambiadores de casco y tubo, las fugas suelen ocurrir en las tapas. Cuando se produce una fuga, es muy probable que resulte en contaminación. Además, la detección de fugas en intercambiadores de calor tubulares es complicada. En muchos casos, se deben tapar varios tubos, lo que puede reducir la eficiencia del equipo en un 30-40%, ya que no se pueden reparar adecuadamente.
Fugas en intercambiadores de placas
Por otro lado, los intercambiadores de placas tienen un diseño que facilita la detección y reparación de fugas. A menos que el golpe de ariete dañe una placa, las fugas no suelen provocar contaminación. En caso de una fuga, el empaque se desaloja, lo que facilita la identificación del problema. Para solucionar la fuga, se pueden usar líquidos penetrantes para localizar la placa dañada, que luego se reemplaza. Una vez reparado, el equipo puede volver a operar con una eficiencia del 98-99%.
Prevención y detección de fugas
- Mantenimiento Regular: La prevención del golpe de ariete se puede lograr mediante un mantenimiento preventivo regular en el intercambiador de calor y el control adecuado de las presiones dentro del sistema.
- Inspecciones Periódicas: Realizar inspecciones periódicas ayuda a identificar signos tempranos de desgaste o daño.
- Monitoreo de Presión: Utilizar sistemas de monitoreo de presión en tiempo real puede ayudar a prevenir los golpes de ariete ajustando automáticamente las condiciones del sistema.
- Diseño Adecuado: Implementar un diseño adecuado del sistema que minimice los riesgos de fluctuaciones bruscas de presión.
Aunque ambos tipos de intercambiadores de calor pueden sufrir fugas debido al golpe de ariete, los intercambiadores de placas tienen una ventaja significativa en términos de detección y reparación de fugas. Su diseño facilita la identificación y reparación de problemas, reduciendo el tiempo de inactividad. Por ello, los intercambiadores de placas son una opción más confiable y eficiente para aplicaciones industriales. |
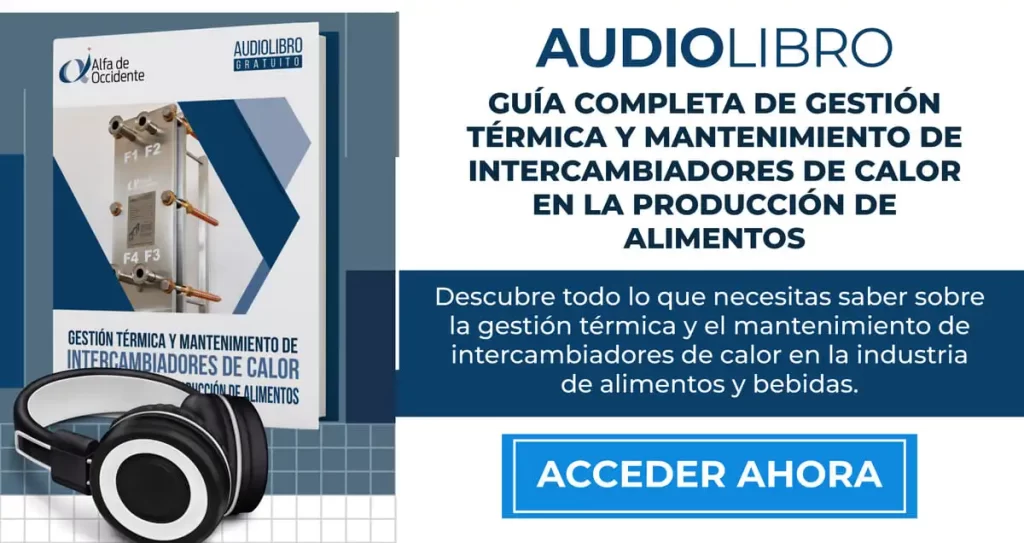
Causas del golpe de ariete y fugas en intercambiadores de calor
Mala operación en el arranque
Uno de los factores principales que causan golpes de ariete y fugas en intercambiadores de calor es la mala operación durante el arranque del sistema. Este problema suele ocurrir cuando se abre la válvula de entrada y se pone en funcionamiento la bomba sin abrir la válvula de salida. Como resultado, el producto no puede pasar debido a la válvula cerrada.
En lugar de detener la bomba y abrir la válvula gradualmente, a menudo se opta por abrir la válvula de golpe. Dado que el aire en el sistema es compresible, este se comprime, mientras que los líquidos no son compresibles y adquieren una velocidad muy alta. Cuando el líquido encuentra un bloqueo, provoca un golpe fuerte, conocido como golpe de ariete.
Impacto del golpe de ariete
Los golpes de ariete son extremadamente peligrosos porque pueden generar presiones hasta 20 veces superiores a la presión de operación, lo cual puede provocar fugas en intercambiadores de calor. Por ejemplo, si el sistema opera a tres kilos de presión, un golpe de ariete puede provocar una presión de hasta sesenta kilos, lo cual puede causar daños severos a cualquier equipo.
En los intercambiadores de calor a placas, el golpe de ariete generalmente provoca que los empaques (juntas o sellos que se colocan entre las placas para evitar fugas de los fluidos que están siendo intercambiados) se desplacen, lo que da lugar a fugas. En los intercambiadores de casco y tubo, la falta de un lugar donde expandirse puede romper los tubos y contaminar el producto.
Otros factores que contribuyen a las fugas
Además del golpe de ariete, otros factores pueden causar daños y fugas en intercambiadores de calor, como el uso inadecuado de productos químicos. Por ejemplo, el ácido muriático, un ácido clorhídrico diluido, puede corroer el acero inoxidable si se usa incorrectamente para la limpieza. Aunque puede eliminar incrustaciones rápidamente, también deja residuos de cloruro que provocan corrosión por picaduras (pitting) en el acero inoxidable, comprometiendo la integridad del equipo.
Prevención y buenas prácticas
- Operación correcta del sistema: Asegurarse de abrir las válvulas de salida antes de poner en funcionamiento la bomba puede prevenir golpes de ariete. Si es necesario ajustar la válvula durante la operación, debe hacerse gradualmente.
- Monitoreo de presión: Implementar sistemas de monitoreo de presión puede ayudar a detectar y evitar situaciones que puedan llevar a un golpe de ariete.
- Uso adecuado de productos químicos: Capacitar al personal en el uso adecuado de productos químicos para la limpieza de los intercambiadores de calor es importante. Evitar el uso de ácidos que puedan dañar el acero inoxidable.
Los golpes de ariete y el uso inadecuado de productos químicos son causas comunes de fugas en intercambiadores de calor. La prevención de estos problemas mediante una operación adecuada y el uso correcto de productos químicos puede prolongar la vida útil de los intercambiadores y mantener su eficiencia. En Alfa de Occidente nos comprometemos a proporcionar equipos de alta calidad y asesoría experta para minimizar estos riesgos y asegurar el óptimo funcionamiento de los intercambiadores de calor. |
Descubra las ventajas de los Intercambiadores de calor a placas
Reduzca costos operativos, aumente la eficiencia y minimice el tiempo de inactividad con nuestros intercambiadores de calor a placas. Contacte a nuestros expertos para una consulta personalizada y descubra cómo nuestras soluciones pueden transformar su Planta.
¿Qué importancia tiene el cambio de empaques para evitar fugas en intercambiadores de calor a placas?
El cambio regular de empaques es esencial para evitar fugas en intercambiadores de calor a placas, sorpresas desagradables, pérdida de producción y paros imprevistos. Basándonos en nuestra experiencia y las condiciones de operación, Alfa de Occidente recomienda una frecuencia de cambio específica para asegurar la continuidad y eficiencia del sistema.
Frecuencia de cambio basada en condiciones de operación
- Intercambiadores que trabajan con vapor: Cuando se trabaja con vapor, los empaques están sometidos a altas temperaturas, lo que acelera su desgaste. En estos casos, es recomendable aumentar la frecuencia de los cambios de empaques para prevenir fallos prematuros y fugas.
- Intercambiadores que trabajan con líquidos: Los empaques sufren menos desgaste cuando se trabaja con líquidos, pero aún es importante monitorear su estado. La frecuencia del cambio puede ser menor en comparación con los que trabajan con vapor, pero no debe descuidarse.
- Impacto de los químicos de lavado: Los productos químicos utilizados para la limpieza de los intercambiadores también afectan la vida útil de los empaques. Algunos químicos pueden ser agresivos y acelerar el deterioro de los sellos, por lo que es esencial considerar este factor al determinar la frecuencia de cambio.
Beneficios del cambio regular de empaques
- Evitar fugas y contaminación: Los empaques desgastados son una de las principales causas de fugas en intercambiadores de calor. Cambiarlos regularmente asegura que el sistema permanezca sellado y operativo.
- Prevenir paros imprevistos: Un fallo en los empaques puede llevar a paros no planificados, interrumpiendo la producción y generando enormes pérdidas. Un programa de mantenimiento preventivo que incluya el cambio de empaques minimiza estos riesgos.
- Aumentar la vida útil del equipo: El mantenimiento regular de los empaques contribuye a prolongar la vida útil del intercambiador de calor, protegiendo la inversión en el equipo.
- Seguridad operacional: Garantizar que los empaques estén en buen estado es una medida de seguridad. Empaques defectuosos pueden provocar fugas de fluidos a alta presión o temperatura, lo que puede ser peligroso para el personal y el entorno.
Recomendación de Alfa de Occidente para evitar fugas en intercambiadores de calorAlfa de Occidente sugiere establecer una regla de mantenimiento que contemple el cambio de empaques anualmente como una medida de seguridad, independientemente del tipo de fluido con el que se trabaje. Esta práctica proactiva ayuda a evitar muchos problemas potenciales y pérdidas económicas derivadas de fallos inesperados.El cambio regular de empaques en los intercambiadores de calor a placas es esencial para mantener la eficiencia, seguridad y operatividad del sistema. Adaptar la frecuencia de cambio a las condiciones de operación y los productos químicos utilizados asegura que el equipo funcione de manera óptima, previniendo paros inesperados, pérdidas de producción y fugas en intercambiadores de calor. |
Cómo detectar fugas en intercambiadores de calor y tiempo de reacción
Detección de fugas en intercambiadores de casco y tubo
Las fugas en intercambiadores de calor de casco y tubo no se detectan inmediatamente porque el fluido del lado de mayor presión contamina gradualmente el lado de menor presión. Por ejemplo, en una planta, si hay una fuga en el intercambiador de calor que calienta jarabe de azúcar, pueden pasar horas antes de que se descubra que el agua de la caldera contiene restos de azúcar. Esta demora en la detección puede dar lugar a una contaminación considerable del sistema antes de que se tomen medidas correctivas.
Detección de fugas en intercambiadores de placas
En cambio, los intercambiadores de calor a placas permiten una detección de fugas mucho más rápida y fácil. Si hay una fuga, ya sea en el lado caliente o frío, es más evidente porque el fluido empieza a escaparse por los empaques entre las placas. Este “lloro” del empaque hace que la fuga sea visualmente detectable de inmediato, lo que permite una intervención rápida para evitar mayores problemas.
Procedimiento de reparación
Cuando se detectan fugas en intercambiadores de calor de placas, el proceso de reparación es relativamente sencillo. Primero, se identifica la ubicación exacta de la fuga. Si no se tienen los empaques de repuesto, se pueden retirar las placas afectadas, cerrar el intercambiador y realizar una prueba hidrostática para asegurarse de que no haya más fugas. Esto permite que el sistema siga operando con hasta un 10% menos de placas, manteniendo entre el 90% y el 95% de la capacidad de producción.
Reemplazo de empaques
Es muy importante que al realizar un paro para el mantenimiento, se reemplacen todos los empaques en lugar de solo los afectados. Los empaques usados tienen una resiliencia menor comparada con los nuevos, y combinar empaques viejos con nuevos puede dañar las placas y causar nuevas fugas. Cambiar todo el conjunto de empaques garantiza una operación continua y sin riesgos.
CONTENIDO ÚTIL: Intercambiadores de Placa tipo Sanitario
¿Qué intercambiador recomendaría un fabricante de calderas para evitar fugas en intercambiadores de calor?
Para un fabricante de calderas, el intercambiador de calor a placas es la elección preferida debido a su eficiencia y fiabilidad. Este tipo de intercambiador no solo mejora muchísimo la transferencia de calor, sino que también reduce el riesgo de fugas, un aspecto de vital importancia en la operación de calderas y sistemas de vapor.
Importancia de los elementos periféricos
En los procesos que involucran vapor, los elementos periféricos son esenciales para una operación eficiente y segura a la vez que se reduce el riesgo de fugas en intercambiadores de calor. Estos incluyen trampas de condesados, válvulas rompedoras de vacío, válvula reductora de presión, sistemas de bypass y controles de temperatura. Aunque estos componentes pueden llegar a costar tres o cuatro veces más que el intercambiador en sí, son necesarios para garantizar que el sistema funcione de manera óptima, manteniendo la temperatura adecuada ayudando a la recuperación de condesados y evitando que el condensado inunde el intercambiador que provocaría la ineficiencia en la transferencia de calor.
Recuperación del condensado
Uno de los mayores beneficios de realizar una buena selección de la trampa de condesados en un intercambiador de placas en sistemas de vapor es el poder recuperar el condensado. Los condensados son extremadamente puros pero también muy corrosivos, y prepararlos para su reutilización en la caldera es un proceso costoso. Recuperar hasta el 95% del condensado puede reducir en gran medida los costos operativos, ya que este líquido, al ser reciclado, no requiere tratamiento adicional y ya está a una temperatura elevada, lo que reduce el costo energético al tener que calentar el líquido que alimenta la caldera.
Ahorro de costos y energía
Evitar fugas en intercambiadores de calor y recuperar el condensado no sólo ahorra en el tratamiento del agua, sino que también implica un gran ahorro en el consumo de energía. Un proyecto típico de vapor puede demostrar que, al recuperar el 90% del vapor desperdiciado, la inversión inicial se recupera rápidamente. Por ejemplo, una inversión de $300.000 MXN podría ser recuperada en menos de un año gracias a los ahorros en costos operativos y energía.
El intercambiador de calor a placas es la recomendación ideal para fabricantes de calderas que buscan evitar fugas y optimizar la eficiencia de sus sistemas. Con el respaldo de un sistema completo de elementos periféricos y la capacidad de recuperar condensados, Alfa de Occidente le ofrece soluciones que garantizan una operación continua, segura y económica, permitiendo a los clientes maximizar su inversión y reducir costos de manera significativa.
Proyecto integral de vaporAlfa de Occidente ofrece a sus clientes no sólo el equipo intercambiador de calor, sino un sistema completo que incluye todos los elementos periféricos necesarios para maximizar la eficiencia y minimizar las pérdidas. Al diseñar un proyecto integral de vapor, se asegura que los clientes puedan recuperar y reutilizar el condensado, ahorrando agua y energía, reduciendo los costos operativos a largo plazo y evitando inundaciones en intercambiadores de calor. |
CONTENIDO ÚTIL – Aplicación de intercambiador de calor a placas en la industria química
Soluciones específicas para minimizar los problemas de fugas en intercambiadores de calor
Mantenimientos periódicos
Una de las soluciones más efectivas para minimizar las fugas en intercambiadores de calor y los riesgos de contaminación es realizar mantenimientos periódicos. Estos mantenimientos deben incluir cambios regulares de empaques, asegurando que el equipo mantenga una operación segura y confiable.
- Cambio de empaques: Los empaques, o juntas, son vitales para evitar fugas en intercambiadores de calor a placas. Se recomienda cambiarlos regularmente según un programa de mantenimiento preventivo para mantener la integridad del equipo y evitar problemas operativos.
- Chequeo de placas: Durante los mantenimientos, es esencial revisar también las placas del intercambiador. Las placas pueden sufrir desgaste o daño que no siempre es evidente. Un chequeo regular permite identificar y solucionar problemas antes de que causen fugas importantes.
Operación adecuada
Además del mantenimiento, la operación adecuada del intercambiador es fundamental para minimizar los problemas de fugas.
- Evitar golpes de ariete: Como vimos anteriormente, los golpes de ariete pueden causar daños graves en los intercambiadores de calor. Para evitarlos, es importante operar las válvulas de manera correcta, asegurándose de abrir y cerrar gradualmente para evitar cambios bruscos de presión. El uso de dispositivos de control de presión y purgadores de vapor también puede ayudar a prevenir estos golpes.
- Arranque correcto del sistema: Durante el arranque del sistema, es importante seguir procedimientos adecuados. Nos referimos a asegurarse de que todas las válvulas estén en la posición correcta antes de iniciar la bomba. Una operación cuidadosa y controlada durante el arranque puede prevenir la mayoría de los problemas de presión que llevan a fugas en intercambiadores de calor.
Soluciones adicionales
- Monitoreo en tiempo real: Implementar sistemas de monitoreo en tiempo real puede ayudar a detectar variaciones en la presión y la temperatura que podrían indicar problemas inminentes. Estos sistemas permiten una respuesta rápida y proactiva, minimizando el riesgo de fugas.
- Capacitación del personal: Asegurar que el personal esté bien capacitado en las mejores prácticas de operación y mantenimiento del intercambiador de calor es vital. Un personal bien informado puede identificar y responder rápidamente a los problemas antes de que se conviertan en fallos mayores.
- Utilización de equipos y productos adecuados: El uso de productos químicos adecuados para la limpieza y el mantenimiento, y la selección de equipos diseñados específicamente para las condiciones operativas de la planta, también juega un papel importante en la prevención de fugas. Evitar productos corrosivos y seleccionar materiales resistentes a la corrosión puede prolongar la vida útil del equipo y reducir las incidencias de fugas en intercambiadores de calor.
Minimizar las fugas en los intercambiadores de calor requiere un planteamiento multifacético que incluye mantenimientos periódicos, operación adecuada y chequeos regulares. Alfa de Occidente tiene disponible para usted soluciones completas que garantizan una operación segura y eficiente de los intercambiadores de calor. Con una visión clara en el mantenimiento preventivo, la capacitación del personal y el uso de equipos adecuados, es posible reducir significativamente los riesgos de fugas en intercambiadores de calor y garantizar la continuidad y la eficiencia operativa. |
Contenido útil: Problemas en Intercambiadores de Calor Tubulares y de Placas para la Industria de Alimentos
Reparación de fugas en intercambiadores de calor
La reparación de fugas en intercambiadores de calor, ya sean de casco y tubo o de placas, es de vital importancia para mantener la eficiencia y la operatividad del sistema. A continuación, te mostramos los pasos y métodos recomendados para afrontar este problema en ambos tipos de intercambiadores.
Reparación de fugas en intercambiadores de casco y tubo
Identificación de la fuga:
- Inspección visual y pruebas de presión: comience con una inspección visual y pruebas de presión para identificar la ubicación exacta de la fuga. Esto puede involucrar la observación de la acumulación de líquidos o el uso de trazadores y detectores de fugas.
Acceso a los tubos:
- Desmontaje de tapas y cabezas: retire las tapas y cabezas del intercambiador para acceder a los tubos internos.
- Extracción del haz de tubos: en algunos casos, puede ser necesario extraer todo el haz de tubos para reparar o reemplazar los tubos dañados.
Reparación del tubo:
- Taponamiento o reemplazo de tubos: los tubos con fugas pueden ser taponados o, en casos más graves, reemplazados. El taponamiento es una solución temporal que puede afectar la eficiencia del intercambiador.
- Soldadura y reacondicionamiento: las fugas en intercambiadores de calor de menor importancia pueden ser reparadas mediante soldadura y reacondicionamiento de los tubos.
Reensamblaje y prueba:
- Montaje de componentes: después de las reparaciones, vuelva a montar todas las partes del intercambiador.
- Prueba de presión: realice una prueba de presión para asegurar que las reparaciones sean efectivas y no haya nuevas fugas.
Reparación de fugas en intercambiadores a placas
Detección de fugas:
- Inspección visual y pruebas hidrostáticas: las fugas en intercambiadores de calor de placas suelen ser más fáciles de detectar mediante inspección visual, ya que el fluido se escapa por los empaques.
Acceso y desmontaje:
- Desmontaje de placas: retire las placas del intercambiador, especialmente aquellas que están alrededor del área de la fuga.
- Identificación de placas dañadas: use líquidos penetrantes para identificar placas dañadas que puedan tener grietas o perforaciones.
Reemplazo de placas y empaques:
- Sustitución de placas: reemplace las placas dañadas por nuevas.
- Cambio de empaques: es altamente recomendable reemplazar todos los empaques durante el proceso de reparación para asegurar un sellado uniforme y evitar futuras fugas.
Reensamblaje y pruebas:
- Montaje de placas: vuelva a montar las placas en el intercambiador asegurándose de que todas estén alineadas correctamente.
- Prueba hidrostática: Es importante realizar una prueba hidrostática para verificar que no haya fugas en intercambiadores de calor y que esté funcionando correctamente.
Prevención de fugas posteriores
- Mantenimiento regular: establecer un programa de mantenimiento regular para inspeccionar y reemplazar componentes desgastados antes de que se conviertan en problemas.
- Monitoreo continuo: implementar sistemas de monitoreo en tiempo real para detectar cambios en la presión y la temperatura que podrían indicar una fuga inminente.
- Capacitación del personal: asegurar que el personal esté bien capacitado en la operación y mantenimiento del equipo para evitar errores operativos que puedan causar fugas en intercambiadores de calor.
La reparación de fugas en intercambiadores de calor es esencial para mantener la eficiencia y la seguridad del sistema. Tanto en intercambiadores de casco y tubo como en los de placas, seguir procedimientos adecuados de detección, reparación y prevención puede prolongar la vida útil del equipo y asegurar una operación continua y eficiente. |